En entornos industriales donde la continuidad operativa es crítica y los márgenes de error cada vez más estrechos, el mantenimiento de los equipos no puede depender exclusivamente de revisiones calendarizadas o de la respuesta a fallas ya ocurridas. En este contexto, el mantenimiento predictivo, impulsado por tecnologías como la telemetría industrial, se consolida como una estrategia clave para anticiparse a los problemas, reducir costos y mejorar la eficiencia global de las operaciones.
A diferencia del mantenimiento reactivo —que actúa una vez que el problema ya se ha presentado— y del mantenimiento preventivo —que se basa en cronogramas fijos sin considerar el estado real del equipo—, el enfoque predictivo se fundamenta en datos reales, recogidos en tiempo real, que permiten detectar patrones anómalos en el funcionamiento de la maquinaria. Esta capacidad de anticipación reduce drásticamente las intervenciones innecesarias, permite programar las que sí son necesarias de forma inteligente, y optimiza la utilización tanto de los recursos humanos como de los activos productivos.
La telemetría como motor del mantenimiento predictivo
La telemetría industrial es el componente tecnológico que hace posible este cambio de paradigma. Mediante sensores instalados en equipos, sistemas e infraestructuras críticas, es posible recopilar información constante sobre variables fundamentales como temperatura, vibraciones, presión, consumo energético o ciclos de carga. Estos datos son transmitidos a plataformas de análisis donde pueden ser visualizados en tiempo real o almacenados para ser estudiados en el largo plazo, identificando tendencias que serían invisibles sin este monitoreo continuo.
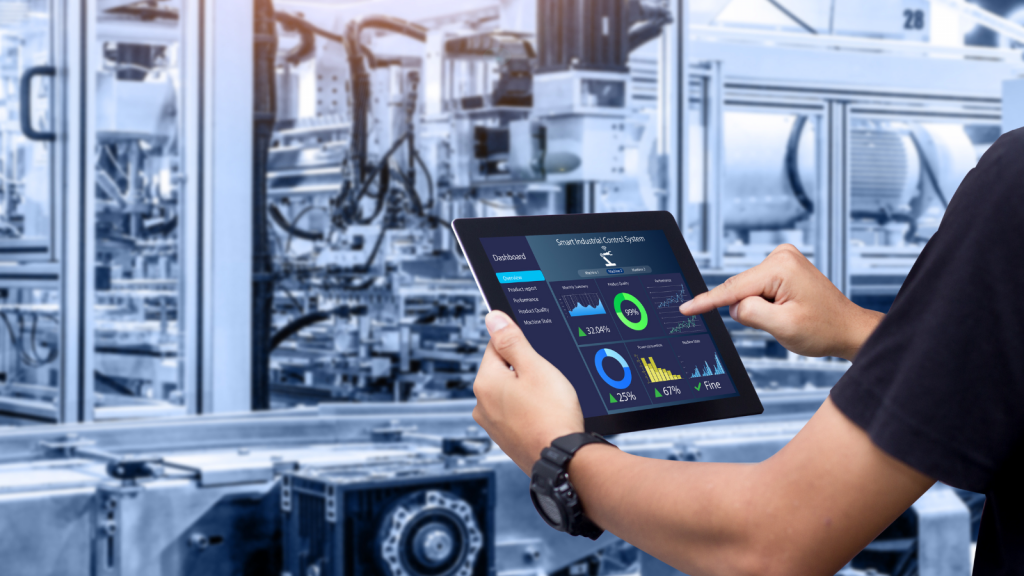
Al identificar desviaciones respecto a los parámetros normales de operación, es posible prever el deterioro de un componente antes de que este genere una falla. De hecho, estudios como el de Smith, Johnson y Patel (2020) muestran que las organizaciones que adoptaron sistemas de telemetría aplicados al mantenimiento predictivo lograron reducir en un 25 % sus costos de mantenimiento, y en un 35 % el tiempo de inactividad no planificada.
Fallas evitables y oportunidades de mejora
La gama de fallas que pueden anticiparse con un sistema bien implementado de telemetría es amplia y relevante. Por ejemplo, un aumento paulatino de vibraciones puede indicar un desgaste incipiente en rodamientos; una elevación sostenida de la temperatura puede ser síntoma de una falla inminente en el sistema de refrigeración de un motor; y un comportamiento errático en los ciclos de carga puede revelar un problema en el suministro eléctrico o en el controlador del equipo.
Gracias al análisis de estos datos, no solo es posible evitar la falla, sino también entender su causa raíz, ajustando el entorno operativo para reducir el desgaste a futuro. Esto convierte al mantenimiento predictivo en una herramienta de aprendizaje organizacional continuo, más allá de una simple estrategia de intervención.
Beneficios estratégicos del mantenimiento predictivo basado en telemetría
Uno de los beneficios más inmediatos es la disminución de las paradas no planificadas, lo cual impacta directamente en la productividad. Cuando una máquina crítica se detiene de forma imprevista, los costos asociados no solo incluyen la reparación, sino también la pérdida de producción, los tiempos muertos de otros equipos dependientes, y muchas veces, el incumplimiento de entregas comprometidas.
En segundo lugar, el ahorro de costos no se limita al momento de la reparación, sino que se manifiesta también en la vida útil más larga de los equipos, en la reducción del consumo energético —gracias al funcionamiento en rangos óptimos— y en la optimización del personal técnico, que puede enfocarse en tareas de mayor valor en lugar de realizar revisiones sistemáticas que muchas veces no detectan fallas reales.
Además, los sistemas de telemetría generan un registro histórico completo y automatizado de cada componente, facilitando auditorías, diagnósticos y decisiones estratégicas a nivel de mantenimiento y planificación de inversiones. Un estudio de TechSolutions (2022) estima que el retorno de inversión (ROI) de un sistema de mantenimiento predictivo soportado por telemetría se logra, en promedio, en menos de 18 meses.
Ejemplo aplicado: Refrigeración industrial con telemetría predictiva
Una planta de refrigeración industrial que opera con compresores de alta capacidad comenzó a observar, a través de su sistema de telemetría, un leve pero progresivo incremento en las vibraciones de uno de sus motores principales. A pesar de que el equipo seguía funcionando dentro de parámetros aceptables, la tendencia era consistente. La alerta generada permitió detener el equipo antes de que se produjera un daño mayor. El diagnóstico técnico reveló un desequilibrio en el eje de rotación, que pudo corregirse con una intervención menor y programada, evitando una falla total que habría implicado no solo altos costos de reparación, sino también una interrupción completa de la cadena de frío.
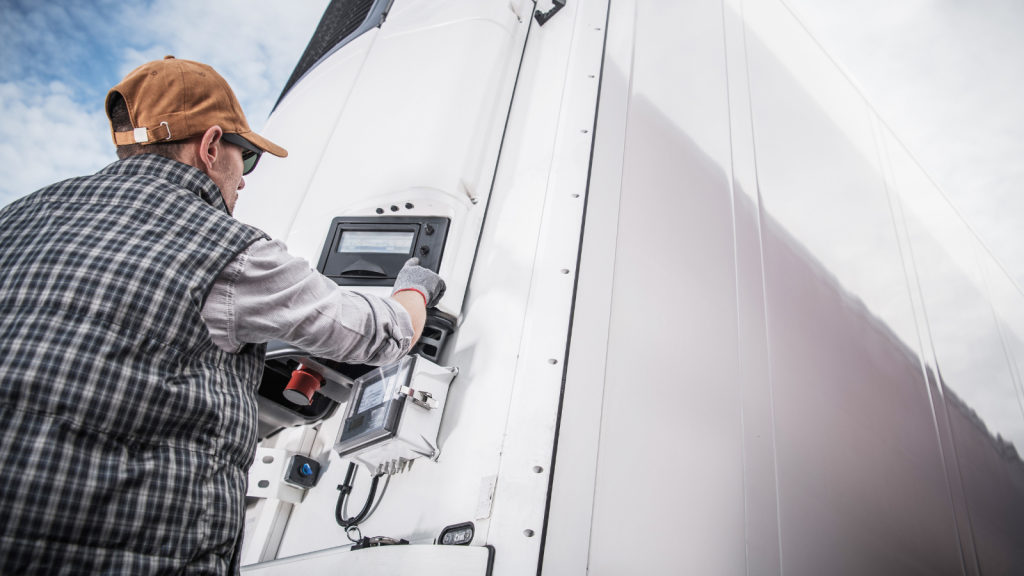
Este caso refleja cómo el mantenimiento predictivo permite actuar con antelación, reduciendo no solo el riesgo técnico, sino también el impacto económico y operativo de una falla evitable.
Pensar en futuro, actuar en presente
El mantenimiento predictivo, habilitado por tecnologías de telemetría, ya no es exclusivo de grandes corporaciones. Hoy está al alcance de empresas de todos los tamaños que busquen operar con mayor inteligencia, reducir incertidumbre, optimizar recursos y proteger sus activos críticos. Incorporar esta tecnología no es solo una mejora técnica: es una decisión estratégica que fortalece la resiliencia operativa y prepara a la organización para competir en un entorno cada vez más exigente.
🔔 Si este artículo te pareció interesante, te invitamos a seguir recorriendo nuestro blog especializado en Telemetría Industrial y soluciones de Monitoreo para la Industria 4.0.
🏭📊 Y si quieres saber cómo un Sistema de Monitoreo Industrial con Telemetría te puede ayudar a reducir costos y hacer más eficiente tu operación MIRA AQUÍ CÓMO FUNCIONA